P-F Curve Explained: Definition and Use Cases in Maintenance
Have you ever heard of the P-F Curve? It sounds like something out of a science fiction novel, doesn’t it? But in reality, this curve is actually quite useful for maintenance.
The P-F Curve is an incredibly useful tool for helping with maintenance activities by allowing you to plan your maintenance strategy more effectively and reduce downtime due to equipment breakdowns.
In this blog post, we’ll explain what a P-F Curve is and how it can be used to help with maintenance. So let’s get started!
What is the P-F curve?
The P-F curve, or Prevention – Failure curve, is a graph used to identify asset reliability and performance over time. It plots the interval between an asset’s potential failure (P) and functional failure (F), which allows you to identify when preventive maintenance measures should be taken.
As an asset accumulates operating hours, its expected failure rate increases. The P-F curve maintenance technique offers a way for you to see the health of equipment over time. It’s an essential tool in developing effective maintenance strategies, as it can be used to predict the optimal balance between planned and corrective maintenance procedures.
The ideal preventive maintenance program maximizes uptime while minimizing cost - this is where Brightly’s Maintenance & Operations solutions can come in handy! Our team of experienced professionals can guide you through the implementation and evaluation of a P-F curve and ensure your system runs at peak efficiency.
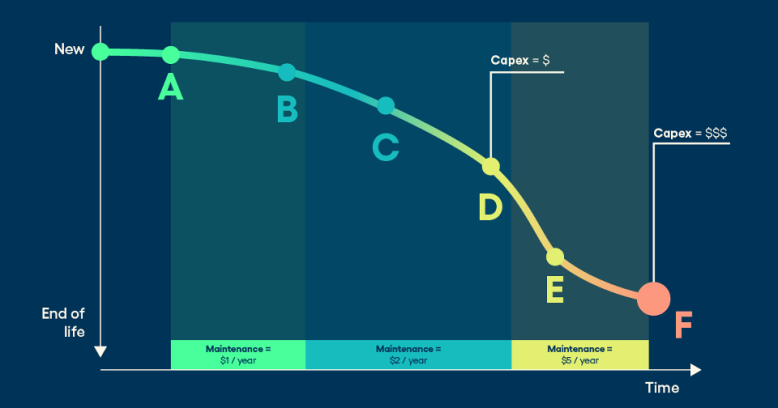
Reliability-centered maintenance
To break things down further, reliability-centered maintenance (RCM) is a systematic method used to help organizations plan and implement effective preventative maintenance schedules. Integral to RCM is understanding the P-F curve, which illustrates the relationship between preventive and corrective maintenance.
In other words, it examines the cost of being proactive versus reactive.
For effective RCM planning, Brightly's Asset Essentials™ solution helps companies with optimizing their assets’ performance and availability. With Asset Essentials' easy-to-use tools, companies have fully traceable asset data, accurate reporting capabilities, and visibility into inventory meaning all maintenance-related information is tracked closely for future reference.
As you might expect, this is critical for ensuring the optimal operation of an organization's assets.
How to read the P-F curve
The P-F curve is an important tool when it comes to analyzing the safe operating range of a piece of equipment. The P-F curve helps engineers identify how well the device works under pressure or other variable conditions and can provide insight into your asset condition-based maintenance needs and potential upgrades needed to reach optimal performance.
Being able to accurately read and understand these curves is essential for proficient technical decision-making and allows you to make informed decisions on what modifications or repairs may be necessary for a particular piece of equipment.
Point P: Potential failure
Point P on the P-F curve is an important element of managing equipment maintenance. It marks the point at which potential failure occurs and this can have severe consequences.
For example, a piece of manufacturing equipment could experience power supply issues at point P, resulting in a sudden break in its operation without warning.
Regular maintenance helps to prevent this type of situation by detecting small changes in performance so that any potential failures can be identified and fixed before they occur. By keeping equipment functioning as intended, it ensures everything runs smoothly and conserves time and money.
Point F: Functional failure
Point “F” on the P-F curve is indicative of functional failure, which can occur when maintenance activities are neglected or not performed properly. This means that if maintenance is not completed and updated regularly, a piece of equipment could eventually experience an unexpected malfunction that results in it ceasing to function altogether.
For example, if a car does not have its oil changed every 3,000 miles as recommended by the manufacturer, then the engine can be prone to experiencing severe damage due to lack of lubrication and overheating, rendering the vehicle useless.
Understanding what point “F” means on the P-F curve is critical for anyone who wants to prevent equipment from experiencing unplanned outages and major malfunctions.
The P-F interval
The P-F interval is a crucial part of the P-F curve and is the most important concept to understand. It directly relates to the amount of time that a maintenance team has between detecting potential failure, and when it actually happens.
Longer P-F intervals mean that more time is available for preventive maintenance practices to be carried out in order to avoid any equipment interruption or breakdowns. Regular condition monitoring and analysis in a time-based system can also help ensure that the P-F intervals remain long so that appropriate reactions can occur before a real failure happens.
How to extend the P-F interval
When it comes to improving or extending the P-F (preventive-to-failure) interval, there are many techniques that engineers and technicians can apply depending on the type of asset, its intended function, and identified failure modes.
The right technique can significantly reduce the likelihood of an unexpected failure occurring, thereby increasing an asset’s service life.
A responsible approach to preventive maintenance extends equipment life and minimizes downtime, which conserves valuable resources. However, in order to do so effectively, it is important to select the correct maintenance method based on a thorough evaluation of your specific requirements.
While not all assets are the same and techniques should be adjusted accordingly, some of the most common maintenance techniques used to identify an asset's condition include:
- Lubricant and sampling analysis
- Corrosion monitoring
- Motor current analysis
- Acoustic emissions detection
- Vibration analysis
- IR thermography
- Process parameter trending
- Process control instrumentation
- Visual inspections
With all these inspection methods at your disposal, you can keep track of the physical condition changes in an asset over time in order to extend its failure interval.
Creating an effective preventive maintenance strategy for assets can be a difficult process and requires specialized techniques.
Despite these complex procedures, organizations can greatly simplify and improve their operations by leveraging solutions such as Brightly Asset Essentials. Brightly allows users to generate proactive maintenance plans and planned maintenance tasks that are customized to specific assets regardless of their industry.
Factors influencing the P-F interval
The failure mode of an asset is largely dependent on a multitude of factors, many of which can be influenced by the design and setup of the equipment. These include the construction materials, the nature and composition of the components, installation techniques, and even moisture and temperature conditions.
Not only that, but external influences such as stress levels and operating environment play a role in determining the P-F interval - the time gap between expected performance and actual failure rate. Thus it is important to consider these factors in order to optimize an asset's life cycle.
Equipment design
Many equipment designs are created with the goal of preventing failure. Design considerations such as safety levels and required maintenance have a significant influence on the P-F interval. As such, the design of a piece of equipment is an integral contributor to potential failure modes, including how quickly they may occur after initial onset and the number or category of failures experienced.
For example, an equipment design could employ automated safety features. This could be done to reduce the risk of a catastrophic failure or it may require regular maintenance to reduce the likelihood of minor complications becoming major issues. Such thoughtful design considerations can improve the P-F interval and provide more reliable performance from the equipment itself.
Equipment use
The P-F interval can be heavily influenced by the use of a piece of equipment. This includes factors such as the frequency with which the equipment is used, whether or not the manufacturer's guidelines and regulations in terms of maintenance and use have been followed, and any periodic impacts that may have resulted from its use.
If any of these variables are misrepresented or unfulfilled - equipment not maintained to manufacturer standards, frequent or poorly managed usage - then the resulting P-F interval can be greatly increased or decreased, depending on the circumstance.
User error
User error is one of the most prevalent factors influencing the P-F interval. Manual errors made during installation, such as leaving out essential components or parts, can drastically reduce the performance and lifespan of an asset.
Similarly, manual mistakes made during operation may lead to higher maintenance costs, reduced functionality, and premature component failure - all of which can have a direct effect on the P-F interval. Properly training operators and engineers in the installation and usage of assets is the simplest way to avoid these technical mishaps and lengthen their reliable and productive life span.
Operational variability
Operational variability is the final factor that greatly influences the P-F interval when it comes to asset maintenance.
How an asset is operated on a daily basis can determine how quickly it wears out, and thus affect repair costs.
Things such as load size, frequency of operation, and what kind of replacement parts are used are important considerations since inefficiencies or poor-quality components can reduce the lifespan of an asset quite significantly.
Over time, the operational variability associated with the asset can have a substantial impact on its available life. Understanding this and taking action to minimize any subpar operations will prolong the life of assets and minimize expensive repairs later on.
How to use the P-F curve for more effective maintenance planning
The P-F curve is a powerful tool for maintenance professionals, as it can help optimize and streamline the planning process.
By analyzing performance metrics over time, it enables proactive and preventative maintenance strategies to be developed. This predictive approach allows problems to be identified and addressed before they cause issues with production, drastically reducing downtime and costs incurred by fixing existing breakdowns.
Leveraging the P-F curve helps maximize efficiency in maintenance operations while still providing quality service at an affordable price. Here are some tips on how to do it.
Schedule preventative maintenance
The P-F curve, or probability-failure curve, is a powerful tool for maintenance teams to plan and schedule preventive maintenance. Using the P-F curve, maintenance workers can identify potential failure modes of their assets or machines in advance and issue preventive maintenance before an inevitable failure occurs. In short, you can schedule maintenance before it becomes a crisis. Your maintenance will be truly preventive rather than corrective maintenance.
This, in turn, allows maximum asset uptime, which is beneficial for both short-term demands as well as long-term efficiency. It also minimizes repair costs due to unexpected breakdowns, which significantly contributes to lower total expenditure on the asset's operation.
In other words, by understanding the probability of failure (and learning how to detect a looming sign of failure) with the help of the P-F curve and implementing preventative maintenance accordingly to reduce risks of errors, one can ensure safety, reliability, and cost-effectiveness - all while maximizing asset uptime.
Identify risks
Maintenance personnel can also use the P-F curve to quickly identify risks associated with assets and their potential functional failures. The points in the curve provide a visual representation of when an asset failure may take place, helping workers prioritize services according to the severity of the risk.
This saves time in the long run by preventing major costly shutdowns or risky, under-maintained assets from being used. By using this type of predictive maintenance planning, maintenance staff can ensure that all assets are monitored, thereby drastically reducing failures and costs.
Extend asset life
By pinpointing the impending failure of an asset, maintenance personnel are better able to schedule routine or corrective measures for system components and optimize the life of those components.
This process can help extend asset life by replacing the component just prior to failure. Ultimately, this enhances productivity and reduces system downtime and cost due to catastrophic failure or unplanned outages.
Establish a maintenance strategy
Planning ahead and taking proactive measures are key steps to ensure effective maintenance operations. The P-F Curve - which visually displays the balance between planned maintenance and repair costs - offers insight into when assets may fail, allowing utilities to plan for these potential outages and establish a tailored approach for their particular situation.
By utilizing the curve’s information, organizations can develop a reliable strategy that best suits their needs, such as when preventive or predictive maintenance techniques should be implemented instead of relying on reactive solutions. Having the data to back up decisions leads to increased efficiency and cost savings that help contribute toward long-term success.
Optimize your maintenance strategy with Brightly’s CMMS solutions
Brightly's computerized maintenance management system (CMMS) solutions are designed to help organizations optimize their maintenance strategies, improve their preventive and corrective maintenance routines, and maximize the P-F interval.
With Asset Essentials, businesses gain access to an easy-to-use platform that allows them to manage work orders, automate preventive maintenance scheduling, monitor inventories and usage patterns, plan overhauls, promote safety best practices and track energy usage.
Through this comprehensive set of CMMS tools, Brightly helps customers reach peak availability levels while reducing costs. If you're looking for a quick and efficient way to bring your maintenance processes up-to-date, Brightly is your ideal partner.
Request a free custom demo with one of our experts today and get started on the path to increased operational excellence.