5 Steps to Strengthen Your Facility Risk Management Plan
Not every emergency is a crisis, but as an employer you have a duty to do your best to address everything that you can with the right tools and practices. Risk management is how you manage safety at the forefront by spending your money wisely to protect employees to do their jobs.
By reducing the number of losses and missed opportunities for safety procedures through proactive work, you’ll actually minimize the overall cost of risk and, in some cases, even lower your insurance premiums.
In doing so, you’ll provide peace of mind for your stakeholders, as well as keep the business safe for both employees and clients. Furthermore, if an emergency does take place (and, more often than not, they will) your business will be better equipped to bounce back and remain in operation after they occur.
However, with your busy day-to-day work and all the tasks you have to do throughout the day, not to mention all the workers whom you manage, in most cases it doesn’t make sense to implement grandiose safety procedures that take an unnecessary amount of time.
Rather, implementing risk management in your facility has to do with common sense, consistency and sustainability.
Benefits of risk management
There are many benefits in the short- and long-term to having a strong risk management program, as it allows you to:
- Reduce actual losses and missed opportunities
- Minimize the cost of risk for your organization
- Provide peace of mind to stakeholders
- Keep the business safe for both clients and employees
- Allow the business to remain in operation after losses
- Lower insurance premiums
Three questions
Risk management impacts both the people on the floor or in the field and those who work in the office. With so many people with a role to play in your safety culture, you have to ask yourself the following three questions:
- Does this safety protocol make common sense?
- Can this safety protocol be done with consistency?
- Is this safety protocol something that we can sustain long term?
Risk management isn’t something that just happens. It’s not as simple as something that we can print out or put on our phones; it’s an in-depth process that takes time.
If there’s a common-sense protocol in place that isn’t done consistently, it won’t be sustained long term, and you’ll see that your gap will increase. The opposite is also true, in that if you’re doing a safety protocol that doesn’t make sense, it naturally won’t be sustained.
The first step to create these protocols is to identify the most common risks in your facility.
Identifying Risk
There’s no such thing as too much training when it comes to risk and safety.
The type of risks you commonly see are most likely top of mind. When it comes to creating a protocol, following a five-step process will ensure that the risks you see are in need of regulation.
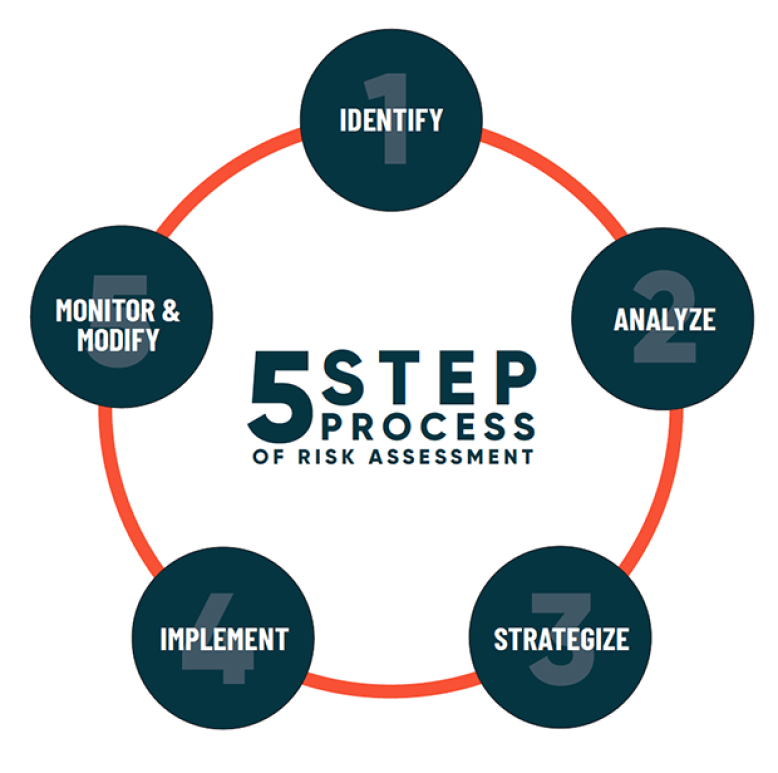
The 5 steps to a better risk management plan are:
- Identify the risk
- Analyze the risk and ensure that it is truly a hazard
- Strategize how to prevent the identified risk
- Implement these processes that will change the risk behavior
- Monitor and modify the risk and processes –and it will only work if you continue this step
Like we mentioned, you most likely already have an idea of what risks are worth noting in your facility.
For example: Maybe you know that your facility’s parking lot frequently gets icy in the winter and that this can pose a hazard for employees driving on and off the premises, as well as walking to the building on the sidewalks. Other times, you may not be sure that a risk is truly a risk – and that’s when frequency versus severity comes in.
Frequency vs. severity
Sometimes, you may not be sure if something poses a risk. An accident that happened in your facility may have been a single occurrence, for instance. In order to determine a risk at this stage, we like to use the frequency vs. severity model.
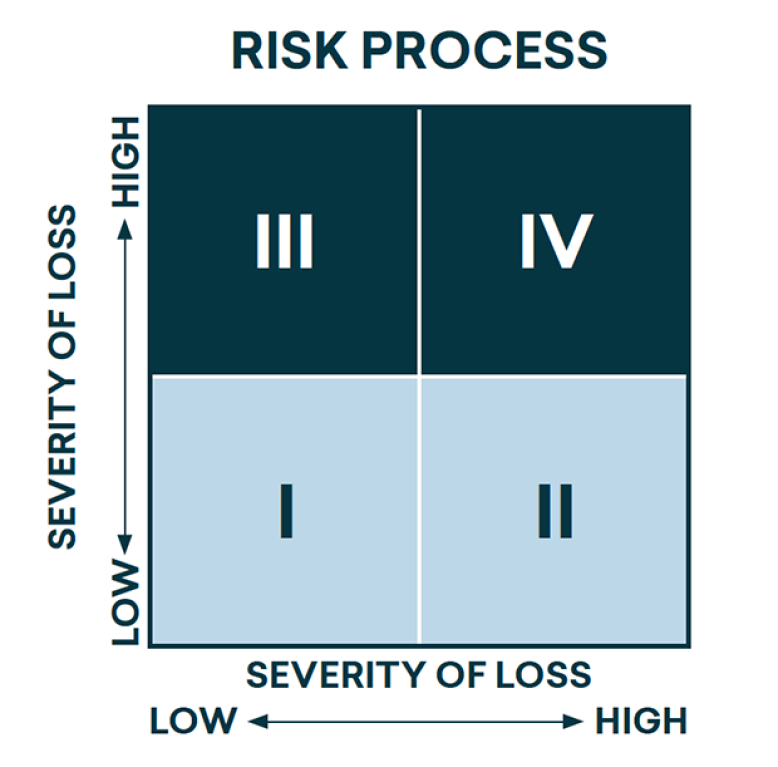
A risk can occur frequently with low severity, and they can also occur infrequently with high severity. Using the chart in Figure 1, you can determine where an accident falls on the chart.
If an accident happens with low severity and low frequency (quadrant I), it’s most likely not going to be as pressing as a high severity and high-frequency accident, or even a low frequency and high severity one. Frequency also refers to the frequency of loss. Higher frequency of loss is always going to go to severity of loss, which means that something more severe when it occurs.
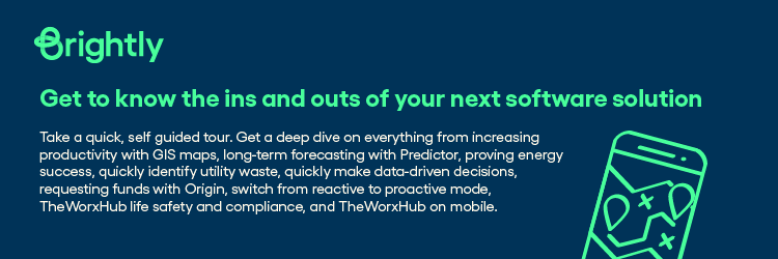
Data collection
One of the best ways to determine where a risk falls on the frequency vs. severity spectrum is through the collection of data. Having an operations management system can help with the accumulation of data, so you can see your risk areas and act on them. Such software can also bring to light a recurring accident that you may not be aware of, and it can help justify modifications to your facility or safety procedures to administrators.
At the end of the day, there are risks in all of these hazards and we need to think about not only the things that happen frequently but also the things that we must insure independently against.
Guidance from the top
When you’re in the planning stage, ensure that you also take your state’s regulations into account. Each organization has individual codes and standards that we need to adhere to per our state, or authority having jurisdiction (AHJ).
Here are some common ones that we all must acknowledge:
Fire Codes
- National Fire Protection Association
- Local fire marshals to come inspect the facilities and become familiar with your buildings and assets
Regulatory Agencies
- OSHA
- EPA
- Division of Health Services Regulations
- NC Dept. of Labor
- FDA
- CDC
- The Joint Commission (for healthcare facilities)
To discover your state’s regulations, OSHA has a full list of regulations on their website.
Barriers to change
As with any change to daily operations, you may find that there are barriers to change in your organization. They can arise anywhere from top management to board members to even the employees who work on your floor or out in the field. The bottom line is, safety culture isn’t top-down – everyone has a role to play, and anyone can spearhead safety and take ownership.
As we mentioned before, some of the key benefits of risk management include:
- Reducing of actual losses and missed opportunities
- Minimizing of the cost of risk for your organization, including lower insurance premiums
- Providing peace of mind to stakeholders
- Keeping the business safe for both clients as well as employees
- Allowing the business to remain in operation after losses
- Maintaining a positive brand reputation
In addition to human resistance to change, there’s also the question of time. Making a change to your organization’s culture, and even the way that it’s structured, is a time-intensive process.
With Brightly's CMMS, for example, you can not only document and gather data for compliance-related work but to also provide employees with a way to easily report potential risks that they spot on the ground floor.
Positive reinforcement
With all the time you invest in creating a safety culture and gathering data, you want to make sure that you are developing a program that not only gets approval from those in charge but also engages your employees. Oftentimes, only focusing on what went wrong instead of finding solutions and celebrating success will only be a detriment to your safety efforts.
As Mavity mentions in his article, only focusing on what went wrong, or those “lagging” and “leading” indicators in your data, isn’t beneficial to creating a positive safety culture. Doing so can actually lead to the inverse effect that you want, as employees may stop reporting risks and safety hazards out of fear of repercussions.¹
Develop a plan for positive reinforcement, such as a reward system for the number of days without incident.
Remember, you want to enforce accountability and personal responsibility, not turn safety into a blame game.
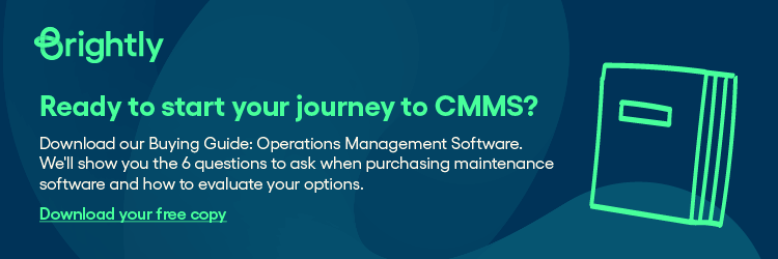
Risk management starts with you
OSHA violations happen, and accidents or emergencies are almost a certainty infacility and operations management. What you can do is encourage and nurture a safety culture in your organization so that everyone has a role to play and is encouraged to focus on safety.
Work culture is about a set of values, beliefs and norms that unite your company together – and safety culture should be no different.
The right risk management plans will support your goals as a company. By being proactive about reducing the number of incidents, you’ll be able to bridge the safety gap.
Ready to start working more proactively to mitigate risk? See how our software can improve risk management with a short conversation.
1