Unlocking the Power of Data in Manufacturing for Efficiency, Quality, and Growth
Many manufacturing industries today face a wave of challenges, from leveraging new and advanced technologies to managing an aging workforce to navigating changing market conditions that can disrupt supply chains. To stay competitive, manufacturers must go beyond traditional strategies and embrace new tools that offer real-time insights and inform decision-making.
And one of the most powerful tools at their disposal? Data.
It might seem simple, but capturing and leveraging data across an entire organization can help manufacturers completely transform their day-to-day, while improving productivity, boosting profitability, and building a more sustainable and resilient future.
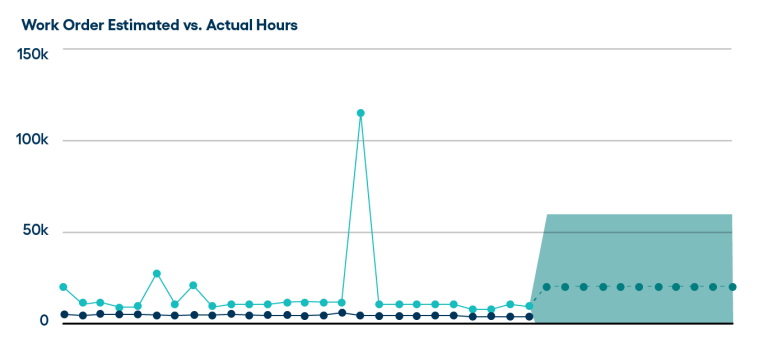
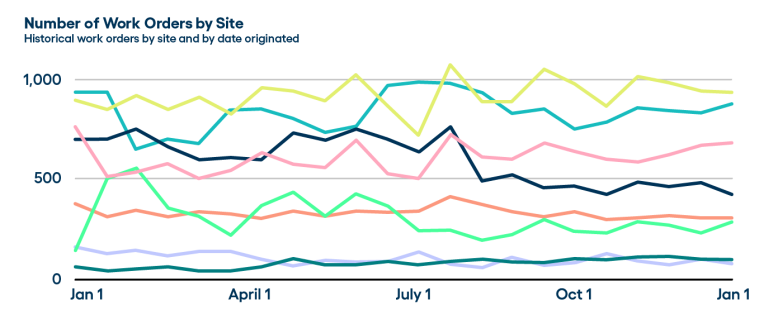
How to effectively utilize your data
To thrive, manufacturers need a clear, end-to-end view of their entire operations and asset histories. Integrating data across departments can give leaders the insights they need to understand performance, spot trends, and make more informed decisions. But data only adds value when it’s used and turning those insights into action is the key to driving growth.
Let’s look at how data can be used effectively across a manufacturing organization.
1. To improve operational excellence
Data can help identify gaps in processes, equipment performance, and workforce efficiency. These insights can reduce waste, minimize downtime, and enhance overall productivity.
2. To enhance equipment reliability
With tools like CMMS, SCADA, and asset lifecycle management software, manufacturers can automate tasks around work order tracking, inventory control, and preventive maintenance. This type of proactive approach can improve overall asset performance and extend equipment lifespans.
3. To enable predictive analytics
Sensor data and machine learning can make it easier to monitor assets in real time, flagging any abnormalities around temperature, vibration, or pressure changes. Using predictive analytics can help prevent unplanned downtime and avoid unnecessary expenses tied to breakdowns
4. To forecast demand
Advanced forecasting tools use historical and market data to predict sales trends and anticipate future inventory needs. These insights can reduce losses from overproduction or expired inventory and support smarter, long-term supply chain planning.
5. To perform root cause analysis (RCA)
Root cause analysis is a systematic process for uncovering the true reasons behind problems. It is a process that can help maintenance and facilities teams uncover underlying causes of recurring failures. RCA data can support more reliable operations and strengthens the case for capital investments or product development initiatives.
6. To improve product quality and R&D
Leveraging data from production lines – like measurements of product size, weight, color, etc. – can ensure quality standards are met. R&D teams can also use this data to improve yields and enhance product design, boosting financial outcomes.
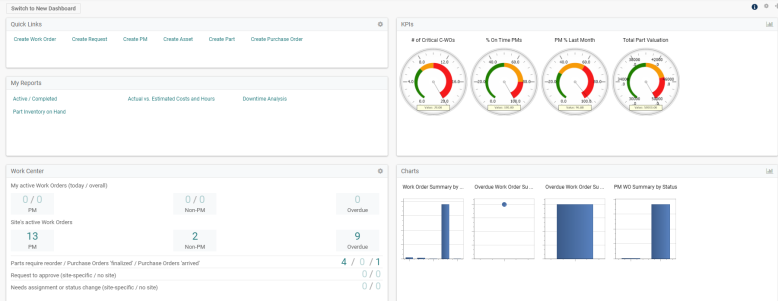
Connecting data across the organization
Data visualization is essential to success in modern manufacturing. With so much diversity and complexity of operations in manufacturing, it can be difficult for organizations to gain a clear view of their performance. But connecting data across departments can help create a more unified picture of the overall business, revealing trends and challenges that may otherwise go unnoticed.
Different roles within a manufacturing environment rely on data in different ways. For frontline operators and maintenance staff, data like shift logs, downtime history, and production schedules help keep lines running efficiently. Providing this information supports their ability to perform daily tasks effectively.
Facilities, maintenance, and plant managers depend on metrics like overall equipment effectiveness (OEE), daily equipment downtime, and throughput to guide operational decisions and improve performance.
At the executive level, company-wide data like YoY production growth, emergency CAPEX funds spend, and monthly P&L numbers help align strategic goals and inform long-term planning. When data is tailored to each layer of the organization, it becomes a powerful driver of productivity, efficiency, and growth.
Conclusion
Data is essential to driving sustainable practices and achieving greater productivity, efficiency, and quality in manufacturing. But its value depends on accuracy—using incorrect data can lead to inefficiencies and confusion.
The ultimate goal for manufacturers should be evolving into a smart factory: a digitally connected operation where systems generate real-time data to empower frontline teams, plant managers, and executives alike.
Want to learn how other manufacturers are using data to transform their operations and improve decision-making? Learn how Siemens Electrical Products used Brightly’s asset lifecycle management solutions to turn data into smarter daily maintenance and lay the foundation for capital planning over the next 15 years.