How to assess your operations for digital transformation
Modern operations require understanding and utilization of digital technology – this is a fact. Imagine getting operations done without any software? Imagine hand-writing checks for invoices and snail-mailing or spending your whole day without using your mobile device. Imagine performing maintenance solely with a paper-based system or spreadsheets. (Does this sound familiar?) While some of us may not be as tech-savvy as others, it would be a lot harder to get our work done. Modern operations aided by technology will go smoother, quicker, more efficient and with less costs as compared to non-aided operations.
A simple maintenance operations example: before using CMMS (computerized maintenance management system), organizations had to reply on manual systems to remind them when to perform preventive maintenance (if at all). Corrective maintenance work orders might be on a blackboard or in a spreadsheet, but difficult to keep updated and organized. The results aren’t great – a reactive, fraught-with-disruptive-downtime environment that frustrates everyone – from maintenance to those who rely on those assets and facilities they maintain.
Fast forward to a modern digital environment and your CMMS will drive these operations. Automatically these systems reminding managers when PMs are due, easily tracking corrective maintenance and efficiently managing maintenance operations. You may have heard the phrase “Industry 4.0” (I4.0). I4.0 has many technologies such as Artificial Intelligence (AI)/machine learning, 3D printing, blockchain, augmented/virtual reality – but the poster child is IoT (the Internet of Things). IoT is technology that allows your asset/facilities to alert you when maintenance issues required intervention, catching minor problems automatically, electronically before they snowball into major disasters. By utilize these amazing tools, you need to progress on your digital maturity journey and create a much better operations workflow.
What is a Digital Maturity Model?
A Digital Maturity Model (DMM) is simply a description of the journey modern operational teams must travel to harness the amazing technologies that aid and optimize our operations. Industry 4.0 technology is a journey – not a destination: I have broken this down into 6 milestones. Along this journey you will find continuous improvement opportunities that will turbo-charge your operations.

Step 1: Computerization
Everyone needs computers these days – not just management. This could be a classic PC, mac or a mobile device. Technicians especially benefit from mobile computing – addressing issues in the field. (I think you have this covered, otherwise you would not be reading this blog!)
Step 2: Connectivity
Connecting computers to each other (networks) as well as to the internet is baseline. Again, you could not read this blog otherwise. Much of our business software these days runs on the internet. In your DMM/I4.0 journey you also need to ensure that your assets, facilities, building and even vehicles are also part of this connection. Connecting operations teams to the physical world allows us to be able to see operational or maintenance status, problems, progress, etc. When our physical assets and buildings can tell us they need help, we can respond quicker. IoT is a big part of this.
Step 3: Visibility
Once humans and the physical assets/facilities are connected we can start to see where help is needed. Some examples:
- A vibration IoT sensor on a pump indicates cavitation issues – sends an alert to the CMMS which requisitions the right technician (with the right instructions, parts, etc.) to fix the problem – well before downtime.
- History of data from assets/facilities can give us operational insights.
All of this will give us faster information to make real-time decisions and improvements.
Step 4: Transparency
With this unprecedented access to our physical world – especially hard-to-reach data - events and conditions become easily available. We can make improvements to our operations like never before. Catching problems early is essential to improving operations. The automated I4.0/IoT technology makes this much easier than the past. In the older days, we either had to guess-and-fix or simply wait for more catastrophic issues. We can make big progress with these insights and transparencies.
Step 5: Predictability
Predictive maintenance (PdM) is the ability to see problems before they happen. Another pump example:
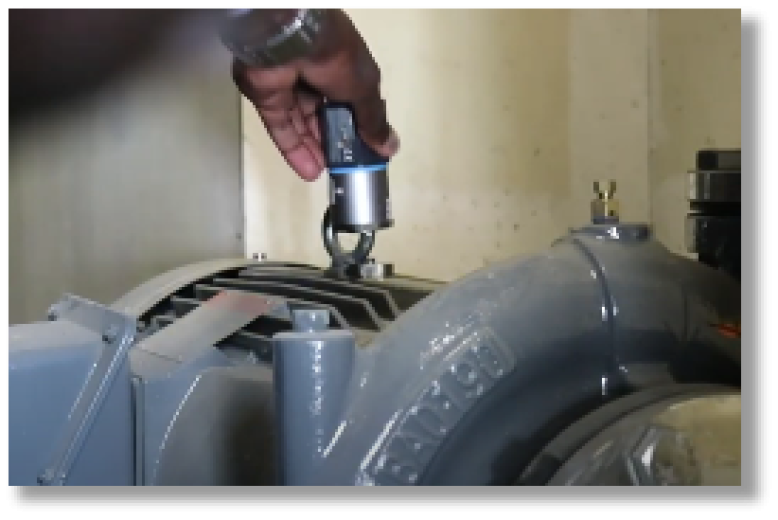
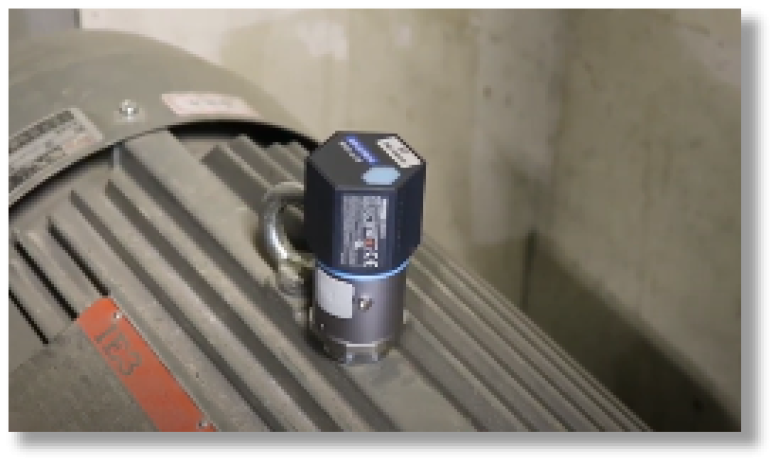
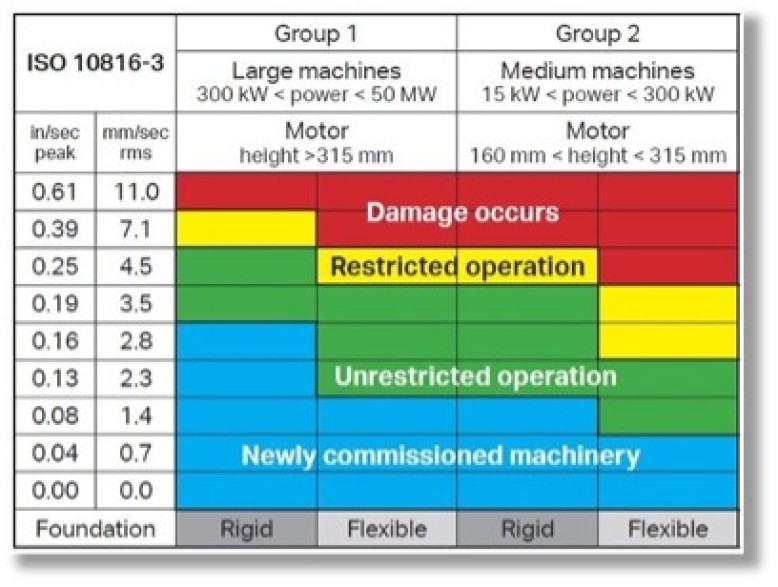
Adding an IoT sensor to a pump allows you to receive electronic data automatically about that pump’s operating status including many metrics including pressure, temperature, vibration and others. In this example, the sensor is broadcasting vibration readings. These readings can be analyzed automatically and electronically. If the readings are outside an acceptable tolerance range, a work order is generated. These IoT-enabled insights are exceptionally aided utilizing AI. This technology allows us to “predict” a problem before it happens, catching problem while it is small before it leads to disruptive downtime.
Step 6: Adaptability
This is the holy-grail for maintenance operations. This is where we utilize all the previous steps to not only predict when issues are happening, but also “prescribe” a solution.
Let’s stay with the pump example: once the IoT sensor/CMMS determine that an issue is occurring, the intelligence can utilize masses of other data:
- Historical similar vibration (and other metrics) readings
- Preventive maintenance history (completed or not)
- Similar issues with the same model pumps (within or outside your operation)
Utilizing AI (Artificial Intelligence) and concepts such “Digital Twins” this intelligence can not only alert us humans to the issue but prescribe the best course of action. This is the essence of “prescriptive maintenance” (RxM). Theoretically, it is possible that remedies to operating issues might be done even without human intervention (turning the pump off, slowing it down, etc.) to keep operations optimal. Again, this is the holy-grail and not many have made it this far. But first, you need to start the journey, or you will never get there!
Conclusion
Industry 4.0 is a journey – not a destination. That journey takes many steps, moving you along the “Digital Maturity Model”. It does not matter where you stand right now, just reading this article is a step in the right direction. Find the right technology partners and continue to make progress in this digital transformation, the benefits can be amazing.
Learn more about our IoT solution, Smart Assets for Asset Essentials™.