A History of Maintenance & How CMMS Has Changed in 200+ Years

It’s called a history “lesson” for a reason. It amazes me how things move in cycles and repeat themselves, even if completely camouflaged in modern technology.
The need to protect our facilities and assets goes back eons. Even our forefathers understood how manufacturing was critical to our nation’s growth, added by proper infrastructure (ports, canals, roads). These lessons ring true today. But have we learned?
A brief history
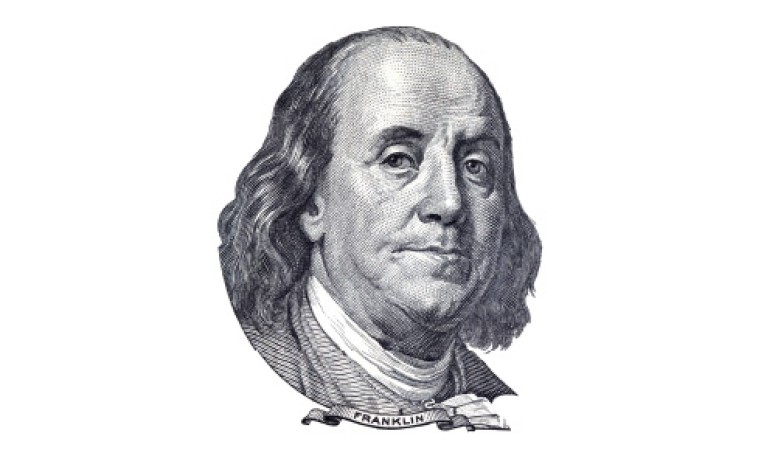
We could go back much further, but my history lesson starts in 1735 (some accounts say 1736) with Benjamin Franklin’s famous quote: “An ounce of prevention is worth a pound of cure” – the mantra of “preventive maintenance.”
A younger Franklin was worried about fires in his now-home city of Philadelphia. Fighting fires in the early 1700s was a tough task and caused a lot of damage, injuries and deaths. Franklin went on a campaign to make improvements: better train the people to fight the fires, have better equipment and tools to battle the blazes, and make preventive measures such as sweeping chimneys. The result: fewer/smaller fires which equates to less property damage, injuries/deaths and a more predictable and enjoyable city life! Sound familiar?
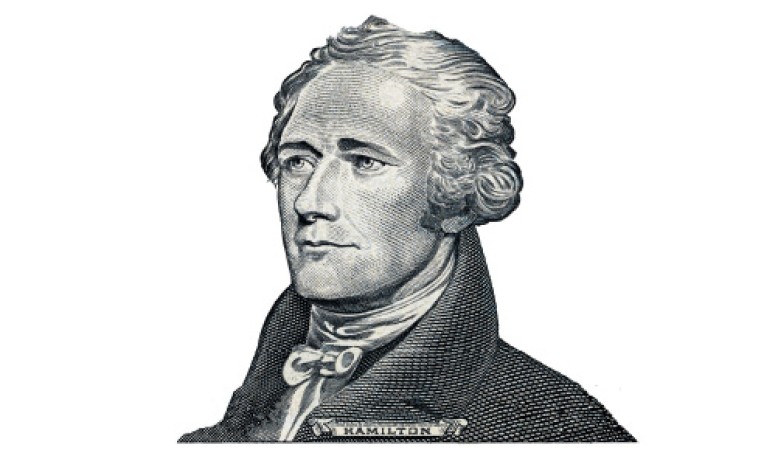
Alexander Hamilton may not have directly been credited with emphasizing “preventive maintenance” at the micro level we see with Franklin, but his more macro views in his “Reports on Manufacturers” (1791) helped shape the “American System,” which became the foundation, growth and success of our industrialized nation.
He was an early champion of industrialization, proper infrastructure and maintenance. Hamilton said: "Bet on manufacturing, technologies, infrastructure, commerce, corporations, finance and banks, and government support of innovation.".
His policies, including sensible use of moderate tariffs used to create subsidies to promote innovation and overall US manufacturing. This promoted technology innovations and employment opportunities. And the movement became the foundation of many things to come. including alignment with the following industrial revolutions. Hamilton understood the critical relationship between manufacturing, supported by critical infrastructure (ports, roads and canals) – all to help America prosper. Again, sound familiar?
The Industrial Revolutions
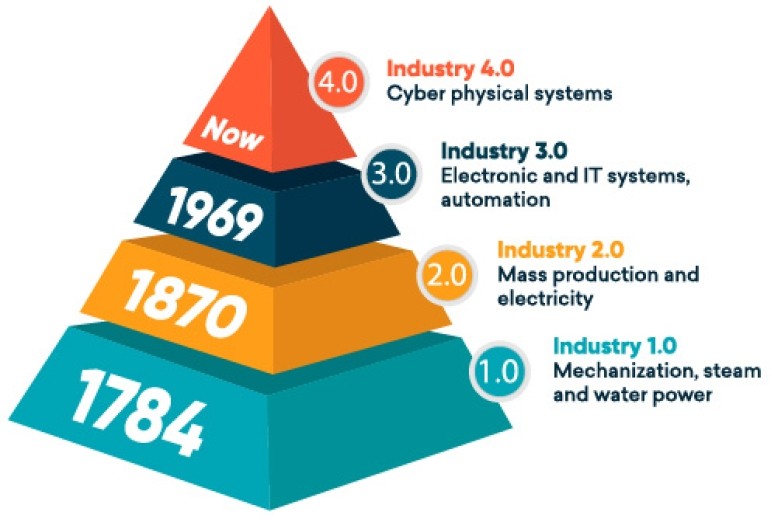
There have been 4 “industrial revolutions” (so far!). Although there were many influences and factors, each revolution had a major technology shift.
The first Industrial Revolution occurred in approximately 1784. The main technology shift was related to mechanization. Up until that point, we had to use human or “beast of burden” power to get any manufacturing done. This revolution occurred when some bright innovators figured out how to harness steam or waterpower to do the back-breaking work humans were doing beforehand. Mechanization, aided by waterpower and steam would move to a factorial increase over human powered.
The second Industrial Revolution started around 1870, when we added electricity to the mix – amazing, nearly unlimited amounts of power. Combined with mass production, manufacturing could now occur at much higher scale. Henry Ford is the poster child for assembly-line/mass production, but that was closer to 1913. Once the investment was made, factories could churn out exponentially more products due to these innovations.
The third Industrial Revolution was in the more recent late 1960s. Robots, computers and other similar automation was at their more primitive dawn, highlighting a profound technology shift. In the following decades, we have watched these technologies completely modernize factories – with faster outputs and safer working environments.
The current fourth Industrial Revolution (estimated to start in 2010) combines all the previous progress, while also employing smart technology to intelligently connect everything: machine-to-machine, people-to-machine, etc. The internet of things (or IoT) is a key part of this revolution, but there are numerous other “exponential technologies” (artificial intelligence/machine learning, additive manufacturing, augmented/virtual reality and much more). The goal is to enable autonomous decision-making processes, monitor assets and processes in real-time – all connecting back to the business enterprise in real time. We are just starting to heat up this revolution.
Manufacturing has metamorphosized all along these revolutions.
Technology is often the impetus, but the goal has mostly been to achieve optimizations, scale, compete and ultimately be more profitable businesses.
I can’t wait to see what the next revolution will be!
The history of CMMS
Computerized maintenance management systems (CMMS) have been around since the early generation of computers. Starting in the 1960s, the first generation of CMMS did not even use a computer monitor but rather “punch cards” running on early IBM mainframe computers.
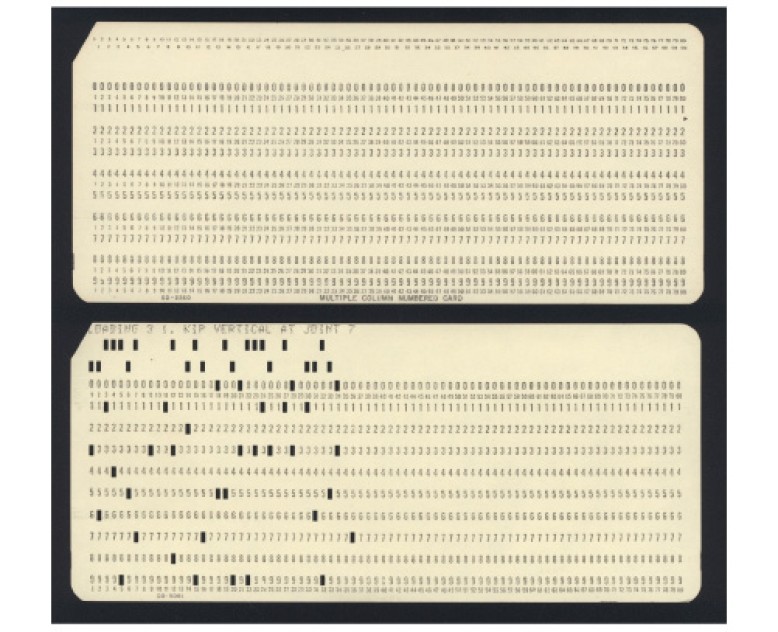
This early version of CMMS was very limited (basic work orders) and used by only very large organizations and government to manage maintenance operations.
In the later 60s and into the early 1970s, computer terminals replaced punch cards. The overall expansion of mainframe computers made CMMS available to more organizations, but remained primitive and still had limited adoption, typically by large organizations and government/military agencies that could afford the technology.
The later 1970s and into the early 1980s saw the introduction of the “minicomputers” (don’t be fooled by the name – they were not that small). These “green screen terminals” started to see continued expansion of CMMS capabilities and allowed large and medium-sized organizations to see the benefit of CMMS.
In the 1980s into the early 2000s, we saw the largest growth of CMMS due to the introduction of the personal computer. These DOS and later Microsoft Windows-based PCs allowed for nearly any size of organization to utilize CMMS. As local area networks became more prevalent, this expanded the abilities and value of CMMS by connecting these PCs together. Eventually, wide area networks (pre- “cloud-based”) allowed for enterprise-level CMMS capabilities.
In the late 1990s and especially from 2000-2010, we saw the next generation of CMMS starting to utilize the world wide web (internet or cloud) to drive maintenance operations. This was truly a monumental breakthrough, as CMMS no longer had to be installed on local computers, but it could be available anywhere you had internet access.
This also changed how CMMS was sold, moving from the historical purchase plus support model to the software as a service (SaaS) or subscription/rental model. Prior to cloud-based software, CMMS was a much larger up-front cost than today’s pay-as-you-use model.
Starting around 2010, as we entered the fourth industrial revolution, second-generation cloud-based CMMS was introduced. This is where we started to see the displacement of the heavier on-premise solutions still running on PCs/servers to complete enterprise-scale internet-based CMMS. Mobile CMMS becomes commonplace, and we start to see extensions into other industry 4.0 technologies with IoT having a major impact.
The past & future of CMMS
What is interesting about CMMS is the core functionality and capabilities have not changed a lot since the early mainframe versions. A heavy emphasis on asset, work orders, parts and procurement have always been in CMMS. For sure, we saw improvements in many aspects of CMMS as the technology improved: reporting/analytics and mobile are good examples.
Over time, we also started to see computers and technology start to model business and industrial operations processes more closely – areas such as condition-based maintenance and reliability-based maintenance. No longer simple “work order lists,” we can now model best practices and methodologies like Six Sigma, total productive maintenance and other “lean” best practices.
The future will continue to make CMMS even easier and more powerful – all part of the smart factory, which is going through a major digital transformation. Assisted, augmented and virtual reality headsets are great examples.
We are truly moving away from simply tracking reactive maintenance. Early generation preventive maintenance (typically based on a calendar) has been improved to use all types of data inputs to become more predictive in nature. Taking conditions and usage metrics from our assets, we can now more intelligently and accurately manage our maintenance operations.
As we continue to develop these technologies, using artificial intelligence (AI) and machine learning (ML), we will start to see even more prescriptive maintenance.
The changing role of the maintenance professional
One of my favorite evolutions of maintenance operations is the changing role of the maintenance person. Calling maintenance in the past was rarely for a good reason. “Call maintenance – my press-brake just crashed!” only to glare at the poor guy coming out of his basement work –area, screaming “get this fixed or our production run is going to be late!” Maintenance was often an underfunded and completely isolated silo that was egregiously underappreciated.
Fortunately, today’s perspective has changed – for the better! The maintenance operations team today is just as responsible for the growth and success of all departments and silos. The maintenance team, aided by technologies such as CMMS, uses a proactive mindset to help increase organizational capacity by reducing unplanned downtime, part stock-outs and team optimization. They help make sure that the entire factory is ready for the rigors and demands of the business.
Positive return on investment
Like most good things for manufacturing, CMMS software is an investment that will ultimately improve operations, control costs, extend the life of your assets and ultimately improve organization profitability. CMMS works hand-in-hand with a lean manufacturing strategy and turbocharged when used in conjunction with best practices like total productive maintenance, 5s, Six Sigma, etc.
If you are not seeing this value from your current CMMS, you need to find the right organization to partner with. The software is important, but make sure your CMMS vendor can also help you with implementation services: consulting, data migration, training and ongoing support are essential to a positive return on your CMMS investment.
Use this guide to help you select the right CMMS.
How history can shape the future
History always comes back around, often proving the same lessons over again. What Ben Franklin and Alexander Hamilton thought was important 250+ years ago rings true today. The lessons of thinking and working proactively, investing in our infrastructure and promoting manufacturing benefit us personally, as manufacturing companies and our overall country.
When you use your CMMS, think back to the early origins of what Franklin set out to do: avoid fires. We can all benefit from less firefighting in our organizations. And let’s be thankful we don’t need to use punch cards to do it!